浅谈连铸小方坯内部质量的控制
发布时间:
2015-04-08 12:31
湖北中钢联冶金工程有限公司 湖北武汉 430023
【摘要】 本文就连铸小方坯的内部质量存在的问题,进一步探讨相关的解决措施。
关键词 连铸小方坯;内部;质量
引言:
在当前,连铸工艺及其相关的配套技术均获得了较大程度的发展,但为了更有效地进行投资与生产成本控制,逐渐降低大方坯应用率而更多采用小方坯已逐渐成为了当前高碳硬线钢生产的重点研究方向之一。在初步的应用实践过程中,高碳钢小截面方坯目前仍受到诸如中心偏析、中心缩孔以及内部裂纹等多方面问题的困扰,继而在很大程度上对方坯的质量构成了非常不利的影响,相关研究指出,由于这些缺陷的存在,将会显着增加发生高碳钢盘条拉拔断裂的几率,针对此方面的缺陷问题进行成因与预防控制措施的分析,为高碳钢小截面方坯的生产提供一定参考。
一、高 效连铸小方坯结晶器
在连铸设备中,结晶器是连铸机的关键部件,钢液通过结晶器壁散热冷却,形成一定厚度的坯壳。目前高 效连铸结晶器一次冷却普遍采用水缝管式结构,水缝作为结晶器冷却水通道,结晶器冷却水以9~12m/s 的速度自下而上从水缝中流过,使结晶器具有良好的冷却效果。
为实现高拉速,要求结晶器具有足够的冷却强度,主要通过采用高 效结晶器铜管和高精度水缝技术实现。高 效结晶器铜管内腔集合形状采用连续锥度或多锥度,以适应铸坯的凝固收缩规律,减小坯壳与结晶器铜壁之间的气隙热阻,尤其是减小角部气隙热阻,增加传热效率;水缝采用高精度窄水缝设计,其宽度一般取3.5~4mm,窄水缝能提高冷却水的流速,水缝高精度可改善水流的均匀性,保证结晶器冷却强度。结晶器一次冷却保证铸坯出结晶器时,形成厚度均匀而强度足够的坯壳,以能抵抗钢液静压力和拉坯力,避免漏钢事故。
初出结晶器下口的铸坯没有完全凝固,只形成一个厚度较薄的(10~20mm)坯壳,中心还是高温液体,需要在结晶器下方设计支撑结构和零段喷淋以支撑和冷却铸坯。目前高 效连铸小方坯结晶器下方普遍采用足辊结构支撑铸坯,并配合适量的喷水以进一步增加坯壳厚度。
足辊装置时在结晶器出口下方四周安装足辊,其安装位置与结晶器铜管对弧,以防对铸坯形成横向应力,对高拉速铸坯初出铜管的薄弱坯壳起支撑作用,减少铸坯变形或漏钢,足辊对拉坯阻力影响较小,足辊调节不当、足辊间隙过大或足辊发生变形均会诱发铸坯菱变。足辊区的喷水冷却属于零段二次冷却系统,时对初出结晶器铜管薄而高温坯壳的辅助支撑和均匀冷却,可增厚坯壳,控制菱变,保证连铸坯质量。
在高速连铸过程中,小方坯发生漏钢事故,冷钢粘结在足辊上导致停浇或划伤铸坯,清理足辊上的冷钢工作比较困难,对损坏的足辊及喷嘴需要更换。
二、连铸小方坯内部质量存在的问题
(一)连铸小方坯中心偏析产生的原因
连铸小方坯产生中心偏析的原因多是因为其中心区域具有C,Mn,P和S等溶质元素分布并不是十分均匀的情况,以至于时常会在铸坯横剖面上表现为铸坯中心处溶质元素的浓度出现峰值,而两边的浓度则相对处于更低的水平,再从铸坯纵剖面上的情况来看,其表观形态存在的形式则更多的表现为V形偏析、U形偏析、点状偏析、线状偏析或是缩孔等,整体来看,沿中心线,溶质元素多呈现出近似周期性的波动。多数时候,连铸方坯中心偏析不足以影响终极产品的质量,在一定范围内是允许存在的。但诸如含碳量相对较高的硬线、钢帘线钢种以及对C,Mn,S偏析更为敏感的抗氢致开裂管线钢种等特殊钢种,中心偏析则将会对其终产品的质量以及加工性能等造成不同程度的影响,故一般被认为是一种非常典型的铸坯内部缺陷。在当前连铸方坯钢种档次持续提升的过程中,铸坯中心偏析的问题实则将愈发的更加突出。
(二)连铸小方坯中心缩孔产生的原因
从工艺方面来看,实践表明中心缩孔的产生多与钢水过热度过高、比水量不妥以及二冷水压不稳等级方面因素关联密切,故需给予这些因素有针对性的改进措施。
三、连铸小方坯内部质量存在问题的解决措施
(一)连铸小方坯中心偏析的方控制措施
1、控制连铸拉素在一定范围内
有学者进行了其他工艺参数不变情况下单纯改变连铸拉速的试验。以观察对中心偏析的影响水平,其试验结果显示,在拉速不断升高的情况下,则铸坯在结晶器内部的停留时间也将会变得越来越短,钢水的凝固时间也相对被延长,铸坯液芯同时变长,这在一定程度上会将等轴晶的形核与长大推迟,柱状晶区也将会被扩大,促使柱状晶“搭桥”,这将造成有更高的几率会形成小钢锭结构,铸坯中心偏析会被明显加重。故可以确定,在将拉速控制在一定相对更理想的范围水平内,连铸方坯的中心偏析问题将得到一定程度改善。
3.改善电磁搅拌工艺
就高碳钢而言,单纯的M-EMS搅拌只能在一定程度将等轴晶区提高,同时也可以在一定程度将中心缩孔减轻,但就其对中心偏析的作用来看,其效果是非常有限的,基于此,采用M+F-EMS的组合搅拌形式是非常有必要的。末端电磁搅拌(F-EMS)所具体发挥的作用比较明显,其不仅可对凝固两相区溶质元素的集聚发挥较好的分散作用,继而减少中心偏析,同时还能在很大程度上减轻中心等轴晶的滑移现象,继而减少办宏观偏析(V型偏析)。但需要注意的是,F-EMS的应用是需要具备一定前提条件的,那就是必须有较宽的中心等轴晶区和使用大功率搅拌凝固末端区域的糊状区,倘若搅拌的强度达不到要求,则所能发挥的效果也是并不十分明显;M+F-EMS联用比较而言是好的,但需保持相对恒定的拉速与稳定的过热度。
4.凝固末端喷水强冷
相关实验性研究结果显示:在现有连铸工艺条件下,铸坯末端喷水强冷与非强冷相比,其对铸坯的中心偏析程度有一定的影响。
(二)连铸小方坯中心缩孔的预防控制措施
1.控制浇钢温度
在进行高温浇注的情况下,柱状晶生长将会得到促进,继而大铸坯中心的搭桥机会也将大大增加,这终有将会导致产生缩孔的几率明显提高。为大程度避免出现高温钢浇注的情况,可以考虑稳定转炉的出钢温度,通过对生产工艺进行妥善调整,以尽量将连铸钢水过热度控制在15~20℃。
2.优化比水量
提速后,为了保证冷却需要,开始时比水量选的较大,铸坯冷却太快,易出现缩孔和裂纹。但比水量太小时,铸坯冷却慢,矫前温度过高,导致坯子带液芯矫直。经过几次摸索,后将比水量稳定在1.45L/kg,铸坯缩孔得到了有效控制。
3.稳定二冷水压
在生产过程中,需对相关工作人员的配水参数给予密切监督,一旦发现有冷水压不稳以及冷却不均的情况,则必须在一时间给予协调解决,不仅要保证有稳定的水压,而且要坚决避免不稳定二冷水压导致形成断续缩孔的情况。除此之外,进一步对零段水量进行统一化的规范要求,同时严格要求不能对水量进行随意调整。
结束语:
在我国现阶段,连铸公司及其相关的配套技术均获得了较大程度的发展,单位了更有效的进行投资与生产成本控制,逐渐降低大方坯应用率而更多采用小方坯已逐渐成为了当前高碳硬线钢生产的重点研究方向,本文就连铸小方坯内部存在的质量问题进行分析与研究,并提高相应的解决措施,有效的促进其快速发展。
下一页
下一页
相关科技成果
联系方式
电话 : 027-83599558 / 83595419
邮箱:csu@csu.net.cn
联系地址:湖北省武汉市江汉经济开发区江兴路17号中信大楼516
办公地址:湖北省武汉市黄陂区卓尔企业社区三期G10栋
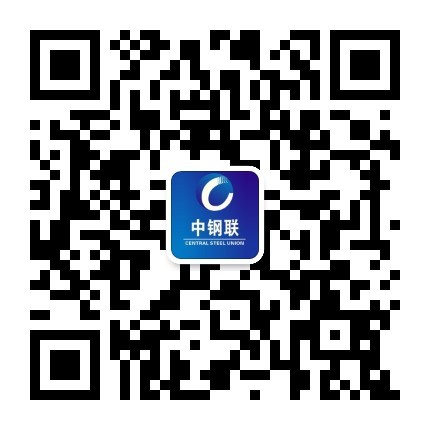
官方微信
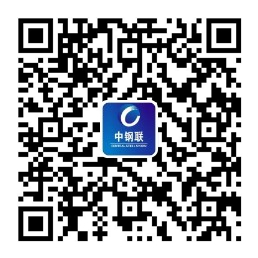
手机网站